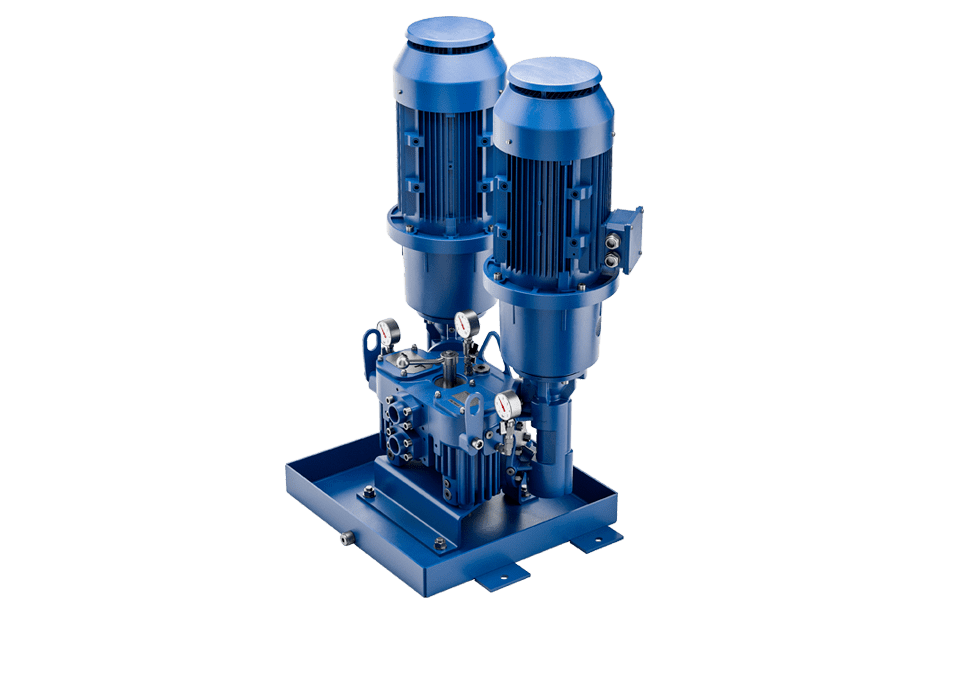
KRAL Pump Stations DKC / DLC / DS/L.
Two pumps provide more than double the advantages.
Cost-effective solution for double the flow rate and for maximum operational reliability.
There are critical applications in which a second screw pump is prescribed for security. With KRAL pump stations you have a cost-effective and space-saving solution with which you can prevent motor standstill, production interruptions and heating failures. Maintenance work can also be carried out during operation without pump standstill.
A further advantage of KRAL double stations is the possibility of parallel operation of the two 3-screw pumps. This means that the flow rate can be doubled, but the space requirement and effort are considerably less than with the installation of two single positive displacement pumps.
Typical applications are booster modules of oceangoing ships, and burner stations in marine and industrial applications. Maximum reliability is required. The most common operating mode is therefore that one screw pump is running and the other is switched off (standby).
Operation, materials, components.
- Delivery rate: 5 to 280 l/min.
- Max. differential pressure: 40 bar.
- Temperature range: -20 °C to 180 °C.
- Housing: Nodular cast iron EN-GJS-400.
- Triple screws: Steel, nitrided.
- Approvals: ABS, BV, CCS, DNV, GL, LRS, MRS, NK, RINA.
- ATEX: II 2 GD b/c group II, category 2.
- Heating: Electrical, media or steam.
- Seal type: Mechanical seal standard or hard material.
- Available with magnetic coupling.
In the case of a ship, the failure of the fuel screw pump in the booster module means that the engine comes to a standstill. If the flame goes out in a burner, a production process will be interrupted or a heating system will fail. Such applications require security. For maintenance, the primary screw pump can be switched to the standby screw pump, without interruption.
Cost reduction through many functions in compact space.
If a second screw pump is necessary, it soon becomes clear that the cost of design, pipework and control is considerable. The space requirement for a structure involving individual components is also very large. A significantly more economical solution is represented by the completely newly developed DKC and DLC dual stations by KRAL. Two screw pumps of the K series up to 16 bar or L series up to 63 bar are fitted to one block. The block integrates all functions within minimum space, and is available with many further options. And the flow rate can be doubled.
Alternate operation between two liquids.
For alternate operation between light and heavy oil operation, for example, the operator does not have to carry out any complex pipework when using KRAL pump stations. As an option, a liquid changeover switch can be fitted. In this way, KRAL dual stations are connected to two pipeline systems with different liquids. Switching between the liquids is manual, electrical or pneumatic. For remote monitoring of the lever position, limit switches are available.
Service without stopping the screw pump.
Reliability through a standby screw pump which is always available is the basic idea of the dual station. In this way, maximum reliability is ensured. After the changeover, the switched-off port of the station block is depressurized and the screw pump can easily be removed. The ship’s engine continues to run, the production process is not interrupted, the heating system continues to operate.
Extremely easy installation.
KRAL dual stations with two 3-screw pumps are quickly set up and fixed. In the simplest case, the suction and pressure lines have to be connected. Done! The connections for the suction and pressure sides are at the front, so they are easy to reach. In contrast to the traditional structure involving two individual screw pumps, apart from connecting the suction and pressure lines no development, design or pipework is required. That saves a lot of time and money.
Various applications.
KRAL double stations with two 3-screw pumps are an economical and reliable solution for all industries in which a continuous supply of oil is required: in oil firing technology for delivering heating oil, circular pipeline transfer screw pumps and burner screw pumps for industrial furnaces, in public buildings and in the ship building industry.
Many useful options are available.
- Heating variants for heating highly viscous fluids.
- Two-way valve for switching between liquids.
- Pressure-retaining valve for constant feed pressure.
- Pressure switch for monitoring pressure.
- Differential pressure display for monitoring the loading of the strainer.
- Temperature measurement of the fluid.
- Monitoring leaked oil.
- Strainer cover protection to prevent accidents caused by oil being sprayed out.
Accessory: KRAL precision flowmeters.
Maintenance work without downtime.
KRAL block aggregates stand out for their ready-for-connection, compact construction. Both of the installed KRAL screw pumps are self-priming pumps with low pulsation and operate at a low noise level. Switching over from the operating screw pump to the reserve screw pump can be carried out electrically or manually. Screw pump maintenance and filter cleaning can be performed without interrupting operations.
Your advantages.
- Reliable solution for many applications.
- High operational reliability.
- Liquid switching without complex piping.
- Doubling of the flow rate.
- Lower costs for design, piping and control.
- Simple installation.
- Service without pump standstill in the system.
- For different pressure ranges, as required.
- Technical data.
DKC series.
Technical data 5-42 55-118 Qth (1450 min-1, 0 bar) l/min 5-43 59-119 Max. pressure at pressure flange bar K 16 16 KFT 16 Temperature °C with NBR rotary lip seal 80 80 with FKM rotary lip seal 150 150 with mechanical seal standard 150 150 with mechanical seal hard material 180 180 with magnetic coupling standard 180 180 with magnetic coupling high temperature 250 250 Viscosity mm²/s min. 2 2 max. 10,000 10,000 Max. pressure at suction flange bar with rotary lip seal 6 6 with mechanical seal standard 6 6 with mechanical seal hard material 6 6 with magnetic coupling 16 16 DLC series.
Technical data 5-10 15-26 32-54 55-85 Qth (1450 min-1, 0 bar) l/min 5-10 15-26 32-58 58-84 Max. pressure at pressure flange bar 40 40 40 40 Temperature max. pumped liquid °C with radial shaft seal NBR 80 80 80 80 with radial shaft seal FKM 150 150 150 150 with mechanical seal standard 150 150 150 150 with mechanical seal hard material 180 180 180 180 with magnetic coupling * Viscosity mm²/s min. 1.5 1.5 1.5 1.5 max. 7,000 7,000 7,000 7,000 Max. pressure at suction flange bar with radial sealing ring 6 6 6 6 with mechanical seal standard 6 6 6 6 with mechanical seal hard material 6 6 6 6 with balanced mechanical seal model LFI/LFT/LFW/LVI/LVT 20 20 20 20 model LFM 6 6 6 6 with magnetic coupling * * customer-specific, contact KRAL DS/L series.
Technical data 5-10 15-26 32-54 Qth (1450 min-1, 0 bar) l/min 5-10 15-26 32-57 Max. pressure at pressure flange bar 6 6 6 Temperature max. pumped liquid °C with radial shaft seal NBR 80 80 80 with radial shaft seal FKM 150 150 150 with mechanical seal standard 150 150 150 with mechanical seal hard material 180 180 180 Viscosity mm²/s min. 1.1 1.1 1.1 max. 7,000 7,000 7,000 Max. pressure at suction flange bar with radial sealing ring 0.5 0.5 0.5 with mechanical seal standard 6 6 6 with mechanical seal hard material 6 6 6 - Models.Double stations DKC and DLC.
The compact double stations DKC and DLC consists of two KRAL screw pumps K or L series, station block, hoisting eye, suction-side pressure gauge, strainer cover, pressure-side pressure gauge, reversing valve lever, vent valve, pressure connection and suction connection. More options on request.
- NPSH
- Operating instructions.