Every drop counts.
System Accuracy of a Fuel Consumption Measurement.
Fuel consumption dominates the operating costs of many companies. In order to save fuel, the consumption values must be determined.
The accuracy of a fuel consumption measurement depends on many different factors, all of which should be taken into account.
In addition to the precision of the individual measuring devices, external influences also affect the accuracy of the measurement result. These include temperature differences between the supply and return lines, fuel pulsations, pipe vibrations and air bubbles in the liquid. If these influences are not taken into account, the measuring error of the system can increase up to 20 % and thus lead to incorrect consumption values.
In a differential measurement, the fuel consumption is determined using the formula "supply flow – return flow = consumption". There are flowmeters in both the supply and return lines. The measuring errors of both measuring devices cannot simply be added together to determine the total measuring error.
The factors influencing the system accuracy in a differential measurement.
Accuracy of the individual measuring devices.
Even if other influencing factors have not yet been taken into account, a system error of 2 % can quickly occur with an accuracy of, for example, 0.5 % of the individual measuring devices.
Temperature difference between flow and return.
Another factor influencing system accuracy is a potential temperature difference of the liquid in the supply and return lines. Especially when measuring the consumption of diesel oil in engines and generators, the temperature in the return line is often higher than in the supply line. The fuel heats up at the consumption device and can be up to 30 °C higher than in the supply line. Since fuel expands when heated, the volume of the liquid changes as a result. In order to avoid additional measurement errors, these temperature and volume differences must be corrected.

Pulsations, pressure surges and backflows.
Fuel does not always flow smoothly and evenly through lines and flowmeters. In a complex pipe system with pumps, engines and valves, pressure surges and pulsations inevitably occur within the liquid.
Such pressure surges cause backflows in the liquid. If these backflows are not taken into account in the flow measurement, an additional measuring error occurs.
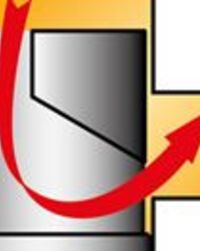
Vibrations of the pipelines.
The use of engines, pumps and valves creates vibrations that spread throughout the entire pipe system. Vibration-proof sensors in the flowmeter help to avoid measurement errors.
Air bubbles in the liquid.
The fuel system is usually a closed system that eliminates air bubbles at an early stage. In some applications, however, air bubbles from the engine get into the return line and thus influence the accuracy of the measurement result. This problem occurs above all with mechanical measuring principles. Air bubbles can be eliminated with air separators.
If all factors are taken into account, you can rely on the accuracy of the consumption values.
A well-founded analysis of the system accuracy of a fuel consumption measurement can be found here: