Lube Oil Pumps for Rotating Equipment.
Everything that moves, whether sliding or rolling, must be lubricated.
But what for? What effects does lubrication have on your machine?
Cost reduction.
The lubricating film protects the components and reduces the cost of maintenance and spare parts.
➔ Saving costs and time.
Friction means loss of energy.
➔ Lubrication saves energy.
Protection.
The lubricating film reduces friction and protects against wear and corrosion.
➔ Increase in service life.
Safety.
The lubricating film dissipates heat. This prevents overheating and protects against massive damage or fire.
➔ No downtime due to destroyed machines.
➔ Fire prevention.
Energy and cost efficiency are at the forefront for operators of rotating equipment. For these reasons, smaller lube oil tanks are increasingly being used for lubrication. The advantages are obvious. Small tanks are cheaper to purchase, take up less space and the volume of lubricating oil is reduced.
This seemingly small change in a plant has implications that need to be considered. The demands on the lube oil pumps increase.
The oil picks up air as it passes through the lubrication points in the machine. When the oil returns to the lube oil tank, most of the air is released. The rate of deaeration depends in part on the size of the tank and the resulting residence time.
Due to the reduced tank volume, the oil stays in the tank for less time, so it has less time to settle and vent. As a result, the lubricating oil contains air pockets as it leaves the tank and an increasing amount of free air as it enters the pump.
Because of their advantages in terms of simplicity and cost, centrifugal pumps are often used for this application. If the requirements increase, as in our example, centrifugal pumps quickly reach their limits because they have difficulties with air pockets in the oil. When the oil enters the centrifugal pump, the pressure drop causes the dissolved air to be converted into free air, which can lead to blockage of the pump's flow - this is called a vapor lock.
The low oil pressure alarm is triggered, there may be a shutdown command from the control system, and in the best case, the standby pump goes into action. If this also fails, the entire system comes to a standstill. The consequences of such a total failure are fatal.
Even if there is no vapor lock, the risk of cavitation is very high. Because when the pressure rises again, the air pockets burst. These so-called implosions damage the pump and reduce the flow rate and thus the performance. The noise and vibrations generated by cavitation also damage bearings, shaft seals and welds.
In screw pumps, the pressure builds up along the screw, allowing the air to escape due to the pump design.
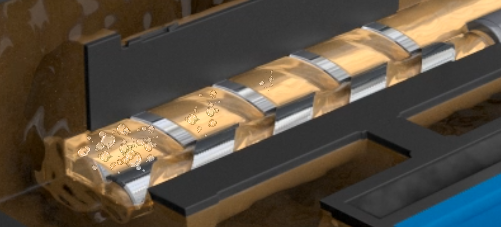
A lot of know-how is required when lube oil pumps for rotating equipment are designed professionally. Experience with the system and plant in interaction with the pump is essential if operation is to run smoothly. Screw pumps deliver the lube oil gently and efficiently. If the pump is designed correctly, low-noise operation is ensured.
03.09.2021