KRAL Pumps Light up Your Life.
KRAL Pumps Light up Your Life!
Yes, you read that correctly.
A bold statement? Admittedly: yes.
But read on. And come to the conclusion that it is true.
Let's go directly to the scene of the action – to the power plant. At least mentally.
The trucks arrive at the power plant terminal early in the morning with their full tanks and wait their turn.
Our first pump comes into action, the unloading pump. The fuel oil, about 30,000 liters per truck, is unloaded. The pumps have to be extremely flexible, because the oils to be pumped have different qualities and viscosities.
Due to their good suction capacity, KRAL pumps are able to suck in the oil by themselves with high force.
The oil is pumped into the storage tank and, as required, is further transported to the day tank by our transfer pumps.
The many different stations in the power plant are already waiting to be supplied by our pumps.
Burner.
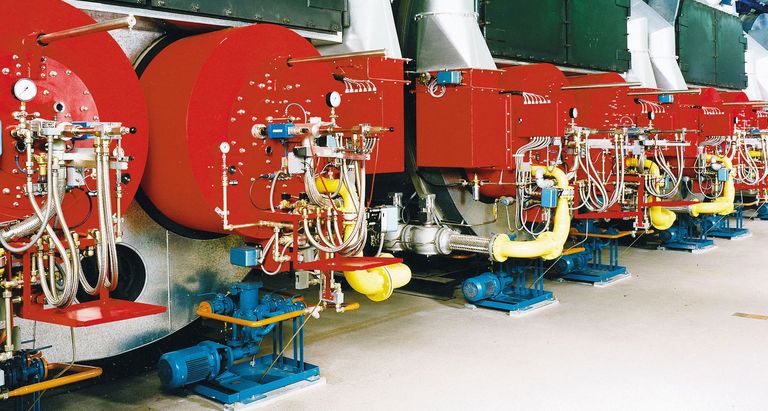
KRAL burner pumps are used to supply these with oil. A precisely metered quantity of fuel must be delivered to the burner nozzle at the right time. KRAL pumps are designed for the high differential pressures that occur in this process.
The firing system burns the oil and thus generates heat.
Steam Turbine.
The heat generated by the burner is used to heat water, which subsequently evaporates. The hot steam drives the turbine. The kinetic energy of the turbine is transferred to the generator, which converts it into electrical energy, i.e. electricity.
Gas Turbine.
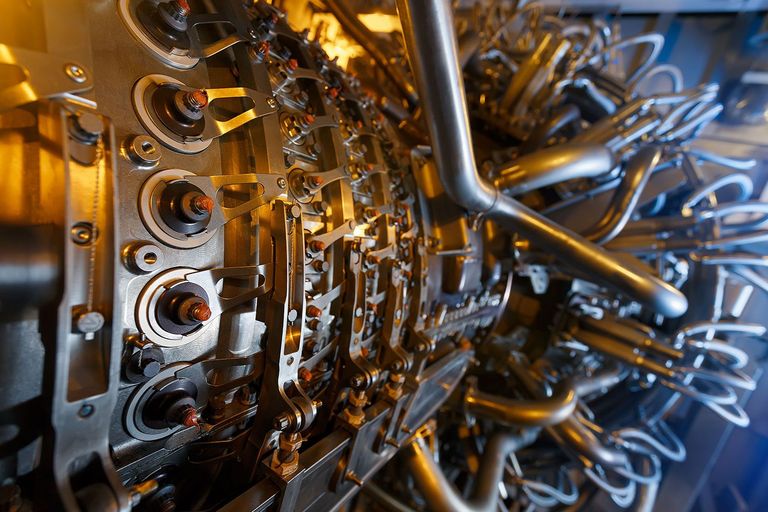
KRAL injection pumps deliver the fuel to the combustion chamber of the gas turbine, where it is mixed with compressed air. The mixture is ignited and burned continuously, producing a hot gas. The gas hits the turbine's blades and sets them in motion – and heat energy becomes kinetic energy. This is then converted into electrical energy by the generator.
KRAL flowmeters regulate the amount of fuel injected. But not only that. They are also used for water injection. This is because only an exact injection quantity achieves the desired result. In this way, our flowmeters make a significant contribution to reducing exhaust emissions. This is because the water lowers combustion temperatures and thus nitrogen oxide emissions.
KRAL lube oil pumps.
The lubricating oil supply to gas and steam turbines plays a central role in the power plant. Constant lubrication ensures smooth operation of the various circuits.
Reduction gears, which are needed to adjust the speed between turbines and generators, must be lubricated.
Power Generator.
Generators can be cooled in various ways, e.g. with hydrogen. The housing filled with hydrogen is sealed gas-tight against the environment by shaft seals. A small gap is created between the rotating shaft and the stationary seal ring. KRAL sealing oil pumps convey the oil, which flows through the gap and thus seals it.
Transformer.
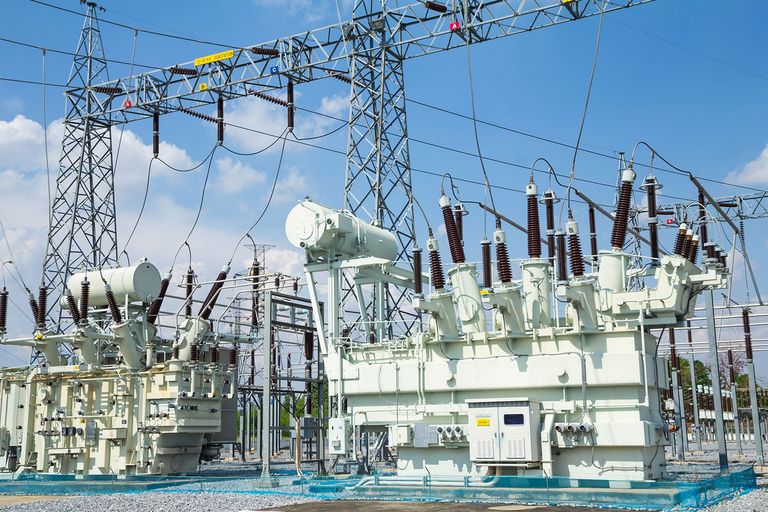
The transformer changes the electrical voltage – increasing or decreasing it as needed. The oil in the housing insulates and cools the winding wires.
The transformer oil must be degassed and dehydrated in the treatment plant. KRAL transformer oil pumps transport the cleaned and filtered oil back to the transformer.
Engine.
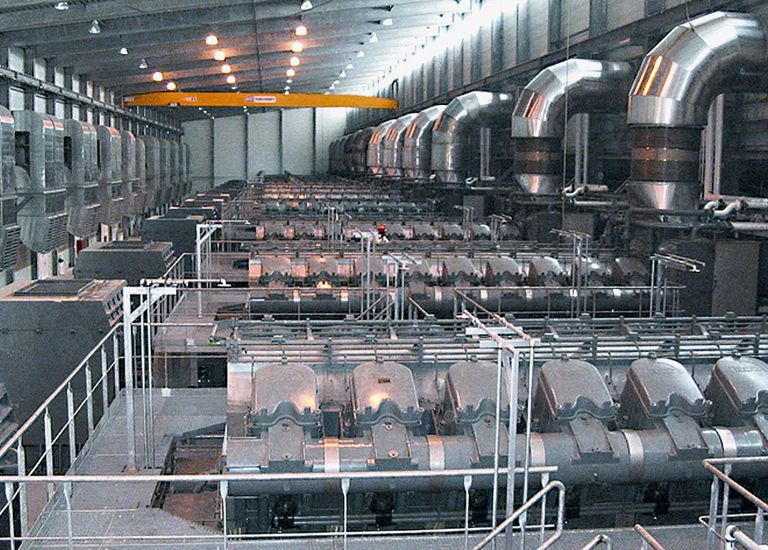
Fuel supply systems.
Engine power plants function with sophisticated fuel supply systems. Separators, boilers and booster modules are supplied with fuel oil and diesel by KRAL supply pumps.
The booster module is the heart of the fuel supply system, because the engine only runs smoothly if the fuel is optimally prepared. The fuel is filtered, pressure, temperature and viscosity are adjusted.
Lubricating oil supply systems.
Recirculating lubrication refers to a lubricant circuit in a closed system.
This not only has the advantage of requiring less lubricant, but none is released into the environment.
The oil acts as a lubricant and coolant. The lubricating oil must dissipate heat and stabilize the temperature at the lubrication points. It also carries away wear particles, prevents corrosion damage and removes condensation.
Water Turbine.
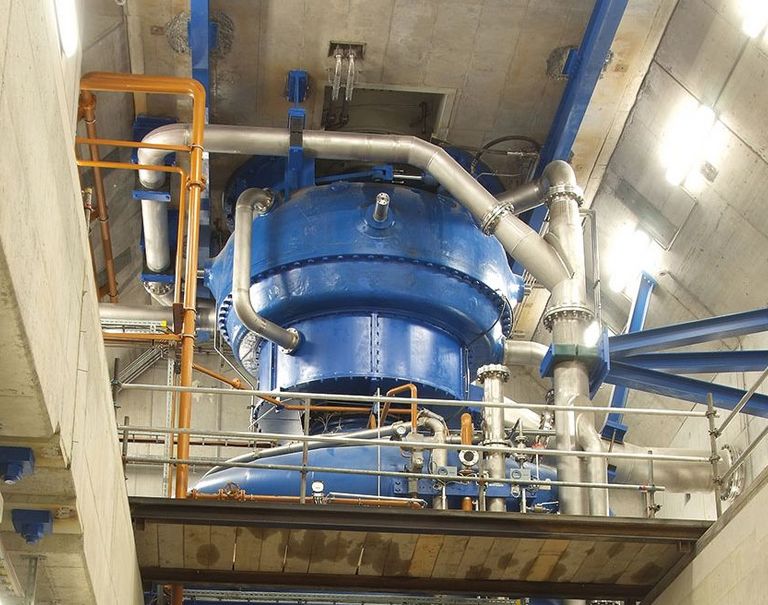
KRAL pumps feed the hydraulics that control the guide wheels of water turbines under a wide range of flow conditions.
KRAL jacking pumps lift the rotor and generator shafts when the turbine starts up. They enable a rapid pressure rise up to 120 bar.
Wind Turbine.
In order to increase the efficiency of the generator in different weather scenarios, KRAL pumps are used for hydraulic adjustment of the wind turbine rotors.
Since gearboxes in wind turbines have to meet high requirements, lubrication plays a particularly important role. KRAL gear lubrication pumps ensure operation, even at extremely high pressures and very low speeds.
All these processes (and many more) are necessary to generate electricity. Every single component in the power plant is important and has its justification.
And so KRAL pumps are also essential components of power plants.
And, do you agree with us now?
KRAL Pumps Light up Your Life!
05.10.2021